Fisher and Paykel appliance holdings ltd are one of the major appliance manufacturers that is owned by a Chinese multinational home appliance manufacturer and supplier Haier. A multinational corporation that is based in East Tamaki, New Zealand. The company was purchased by Haier back in 2012 and offers ovens, fridges, cooktops, dryers, and other related appliances.
For those looking for a clean and contemporary kitchen, you cannot go wrong with Fisher and Paykel refrigerators. Offering you some of the best contemporary kitchen appliances that match your needs and aesthetics. All the while enjoying an appliance manufactured and designed by one of the world’s leading manufacturers.
To help ensure you never face an issue when using your Fisher and Paykel refrigerator we suggest you note down any error code when it shows up, and check is using the Fisher and Paykel refrigerator error codes list below. This will let you know exactly what is wrong, and how to best deal with the situation.
Codes Table
If there is a problem with your appliance, please check the following points before contacting your local Fisher & Paykel Authorised Repairer or the Customer Care Centre.
Fault Code | Explanation |
---|---|
1 | Module failure |
2 | Defrost issue |
3 | Temperature sensor issue |
4 | Temperature sensor issue |
5 | FC sensor issue |
6 | FC sensor issue |
7 | Evaporator sensor |
8 | Evaporator sensor |
9 | PC sensor issue |
10 | PC sensor issue |
11 | Ambient heater/PC, FC fan issue |
12 | Ambient heater/PC, FC fan issue |
13 | Ambient heater fault |
14 | Ambient heater fault |
15 | PC fan issue |
16 | PC fan issue |
17 | FC fan issue |
18 | FC fan issue |
20 | Flapper heater issue |
21 | Flapper heater issue |
22 | Water tank sensor issue |
23 | Water tank sensor issue |
24 | Ice tray sensor issue |
25 | Ice tray sensor issue |
26 | Ice maker motor issue |
27 | Ice maker motor issue |
28 | Ice maker solenoid issue |
29 | Ice maker solenoid issue |
30 | Display harness issue |
31 | Display harness issue |
40 | Ice maker solenoid issue |
41 | Ice maker solenoid issue |
42 | Ice maker fill tube issue |
43 | Ice maker fill tube issue |
49 | Electronic communication error |
Display Features
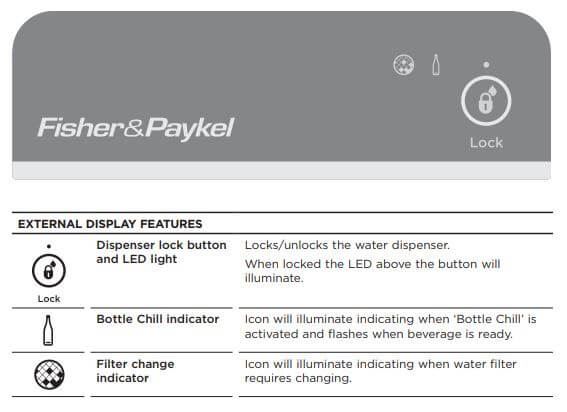
RX Series Refrigerator Codes
Fault Code | Explanation |
---|---|
F1 | PC Sensor issue |
F2 | PC Sensor issue |
F3 | Ambient sensor |
F4 | FC sensor issue |
F6 | Defrost sensor issue |
E0 | Electronic communication error |
E1 | FC fan motor issue |
E2 | Evaporator fan motor issue |
Ed | Defrost system failure |
Refrigerators (Ice & Water) Codes
Fault Code | What to Do |
---|---|
F2 | Defrost fault |
F15 | Fridge fan |
F17 | Freezer fan |
F20 | Flapper heater fault |
F24 | Ice maker sensor |
F30 | Display Fault |
Troubleshooting
This troubleshooting chart on the following pages contains symptoms that may be seen in malfunctioning units. Each symptom is accompanied by one or more possible causes and by a possible remedy or test to determine if components are working properly.
Symptom | Possible Causes. |
---|---|
Unit does not run. | No power to unit. |
Faulty power cord. | |
Low voltage. | |
Faulty motor or freezer temperature control. | |
Faulty relay. | |
Faulty compressor. Is the cabiinet in defrost Mode? | |
Faulty overload. | |
Fresh food compartment too warm. | Excessive door opening. |
Overloading of shelves. | |
Warm or hot foods placed in cabinet. | |
Cold control set too warm. | |
Poor door seal. | |
Fresh food compartment airflow. | |
Interior light remains on. | |
Faulty condenser fan or evaporator fan. | |
Faulty compressor. | |
Fresh food compartment too cold. | Fresh food compartment temperature control set too cold. |
Fresh food compartment airflow not properly adjusted. | |
Freezer and provision sections too warm. | Temperature controls set too warm. |
Poor door seal. | |
Dirty condenser or obstructed grille. | |
Faulty control. | |
Refrigerant shortage or restriction. | |
Freezer section too cold. | Freezer temp control set too cold. |
Faulty control. | |
Cold control capillary not properly clamped to evaporator. |
Troubleshooting Flow Chart
Symptom | Possible Causes. |
---|---|
Unit runs continuously. | Temperature control set too cold. |
Dirty condenser or obstructed grille. | |
Poor door seal. | |
Interior light remains on. | |
Faulty condenser fan or evaporator fan. | |
Faulty control. | |
Refrigerant shortage or restriction. | |
Refrigerant overcharge. | |
Air in system. | |
Unit runs continuously. Temperature normal. | Ice on evaporator. |
Unit runs continuously. Temperature too cold. | Faulty defrost thermostat. |
Noisy operation. | Loose flooring or floor not firm. |
Cabinet not level. | |
Tubing in contact with cabinet, other tubing, or other metal. | |
Drip pan vibrating. | |
Fan hitting another part. | |
Worn fan motor bearings. | |
Compressor mounting grommets worn or missing. Mounting hardware loose or missing. | |
Free or loose parts causing or allowing noise during operation. | |
Frost or ice on evaporator. | Defrost thermostat faulty. |
Evaporator fan faulty. | |
Defrost heater remains open. | |
Defrost control faulty. | |
Open wire or connector. | |
Refrigerant shortage or restriction. | |
Unit starts and stops frequently (cycles on and off). | Loose wire or thermostat connections. |
Supply voltage out of specification. | |
Overload protector open. | |
Faulty compressor motor capacitor (some compressors do not require motor capacitor). | |
Faulty fan motor. | |
Restricted air flow. | |
Refrigerant shortage or restriction. | |
Compressor hot. |
Compressor Does Not Turn On
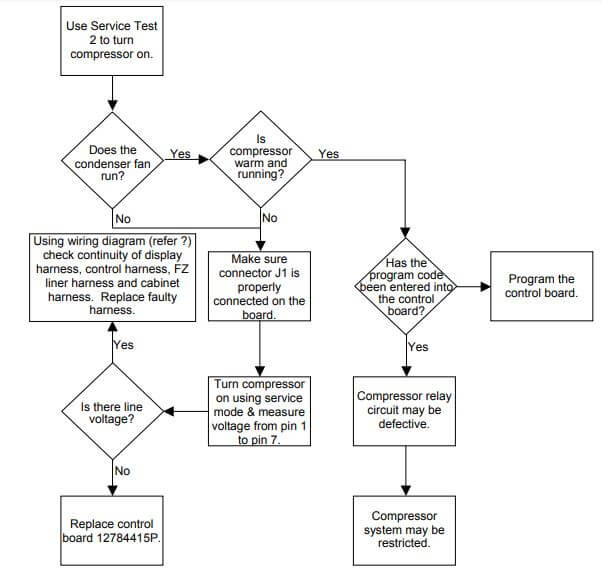
Evaporator Fan Does Not Turn On
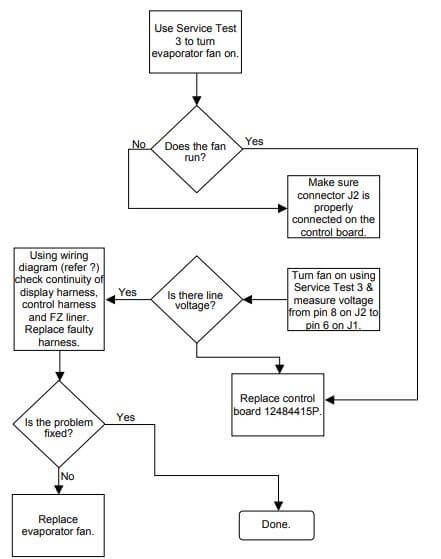
Damper Does Not Move
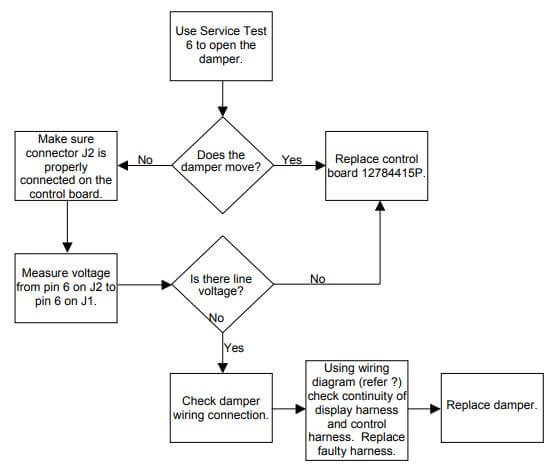
Damper Opens and Never Closes
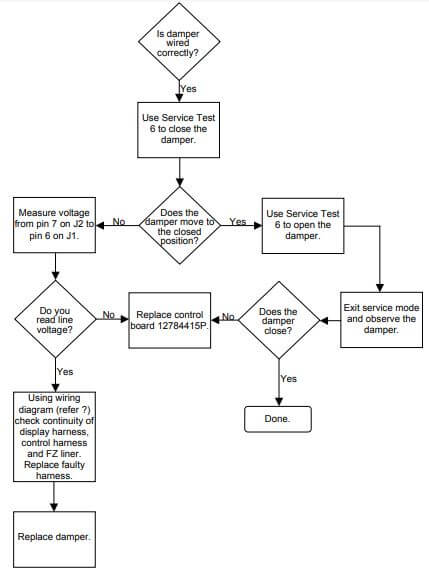
Flashing Display at Power Up
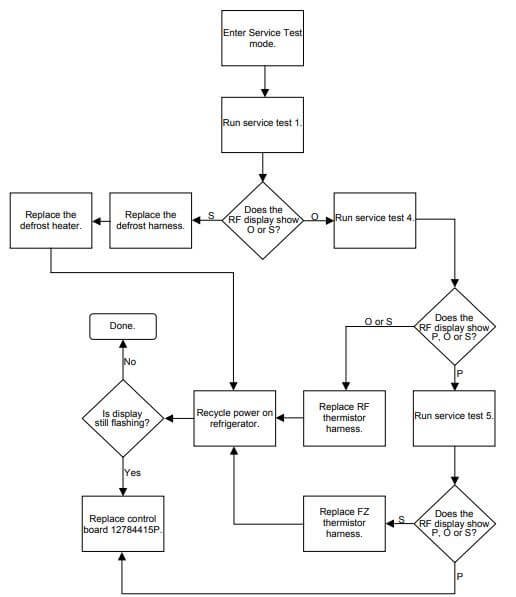
Manual
source: www.fisherpaykel.com