Franke coffee machine error codes are designed to monitor the device’s performance and assist users in quickly identifying issues. These codes can help users troubleshoot machine-related problems more easily, contributing to the longer-lasting, trouble-free operation of the device. In this article, we will examine the meaning and usage of Franke coffee machine error codes.
Codes List
Error Codes | Solutions |
---|---|
009 | Brewing unit motor timeout. The number of increments registered while the brewing chamber was moving is too small. Please restart the system. – Restart the system – Check the incremental sensor – Check the motor – Clean the brewing unit with a brush. |
010 | Brewing unit motor timeout. The number of increments registered while the brewing chamber was moving is too small. Please restart the system. – Restart the system – Check the incremental sensor – Check the motor – Clean the brewing unit with a brush. |
011 | Brewing unit motor timeout. The number of increments registered while the brewing chamber was moving is too small. Please restart the system. – Restart the system – Check the incremental sensor – Check the motor – Clean the brewing unit with a brush. |
012 | Brewing unit motor timeout. The number of increments registered while the brewing chamber was moving is too small. Please restart the system. – Restart the system – Check the incremental sensor – Check the motor – Clean the brewing unit with a brush |
013 | Brewing unit motor timeout. The number of increments registered while the brewing chamber was moving is too small. Please restart the system. – Restart the system – Check the incremental sensor – Check the motor – Clean the brewing unit with a brush |
014 | Brewing unit incremental sensor. More than one negative increment was registered. The brewing chamber is moving in the wrong direction. Please check the wiring of the incremental sensor. – Restart the system – Check the incremental sensor – Check the motor – Clean the brewing unit with a brush. |
015 | Brewing unit motor timeout. A motor timeout occurred during cleaning. – Restart the system – Repeat the cleaning cycle. |
027 | Brewing unit locking mechanism. The brewing unit is not locked. |
028 | Brewing unit missing. |
030 | Initializing brewing unit. During initialization, an error occurred when the brewing unit was being recalibrated. – Restart the system – Check the incremental sensor – Check the motor – Clean the brewing unit with a brush. |
048 | Brewing unit brewing chamber open. The brewing process was canceled because the brewing chamber was able to be opened up too far. Please select a new product or restart the system to recalibrate the brewing unit. – Select a new drink (the brewing unit will be recalibrated) – If this occurs more than once, check the values, see Programming, Menu item 5.2 Brewing unit. |
049 | Brewing unit brewing chamber open. The brewing chamber could not be closed. Please check the grind quantity and select a new product. – Select a new drink (the brewing unit will be recalibrated) – Check the grind quantity – Check the calibration of the grinders, see Programming, Grinder 1 - 3. |
060 | Fill Boiler 1. The boiler with heater 1 could not be filled. Please restart the system. – Restart the system – Check pump pressure, Commissioning, Menu item 0.3 Set pressure – Check the boiler 1 (coffee) pressure relief valve for leakage (water flows into drip tray) – Check water supply (leaktightness and supply) |
061, 062 | Fill Boiler 2. The boiler with heater 2 could not be filled during operation. The heater will be switched off. Please restart the system. Please restart the system. – Restart the system – Check boiler 2 (hot water) pressure relief valve for leakage (water flows into drip tray) – Check the continuous level sensor (connection/ limescale formation), Programming, Menu item 5.10 Individual inputs – Check water supply (leaktightness and supply) |
079 | The brew boiler's water flow is disrupted. The flow meter receives too few or no impulses. Please restart the system or select a different product. – Check the grind coarseness (must not be too fine) – Check the product settings – Select another product – Check the flow meter. |
080 | Flow meter error 2. The water flow of the tea boiler is disrupted. The flow meter receives too few or no impulses. Please restart the system or try a different product. – Check the product settings – Select another product – Check the flow meter – Open the shut-off valve. |
081 | Flow meter error 3. The water flow of the cold water bypass is disrupted. The flow meter receives too few or no impulses. Please restart the system or try a different product. |
082 | Flow meter error 4. The water flow in the Iced Coffee Module is disrupted. The flow meter receives too few or no impulses. Please restart the system or try a different product. |
083 | Flow meter error 5. The cold water flow is impaired. The flow meter receives too few or no impulses. Please restart the system or try a different product. |
087 | Initializing water line. No 100 ml could be dosed through the brewing valve and the bypass valve within 25 s during initialization. Please check the water supply and restart the system. Restart the system – Check water supply (leaktightness and supply) – Check the water circuit for leakage. |
088 | Initializing steam boiler level. During initialization, the minimum steam boiler level could not be achieved within 25 sec. The steam boiler continues filling. If the level still has not been reached after 4 minutes, another error message appears. In this case, please check the water supply and the level sensor. – Wait at least 4 minutes – Check the continuous level sensor and replace if necessary – Check water supply (leaktightness and supply) – Check the water circuit for leakage. |
090 | iQFlow needle valve. The iQFlow needle valve is not working properly. Restart the system. |
091 | iQFlow needle valve. The iQFlow needle valve is not working properly. Restart the system. |
092 | Needle valve/brewing unit tightness. The iQFlow needle valve cannot be closed or the brewing unit is not completely tight. |
093 | iQFlow initialization. iQFlow has been initialized. |
094 | Brewing module may be leaking. The brewing module may be leaking. Check the brewing module. Check the brewing module for leakage. |
096 | Steam boiler level sensor. Steam boiler. |
101 | Hardware error on the FoamMaster. A hardware error (short circuit) has occurred on the FoamMaster controller. – Check the connection cable – Check the connection with other CAN nodes, Programming, Menu item 5.9 Individual outputs (test menu CAN bus) – Check the connection cable. |
102 | FoamMaster software out of date. The FoamMaster software is out of date. Please update the FoamMaster software to the current version using the service tool. Update the FoamMaster software to the current version using the Service Tool The minimum required version will be displayed. The exported outof-date software version of the milk control can be displayed in item 0.10 System information. |
104 | Milk flow affected. The flow meter receives too few or no impulses. Prepare another product. Restart the system. – Select a new product – Restart the system. |
105 | Thermoblock. Heating tendency recorded. |
106 | Milk flow meter. The milk flow meter (B11) was measured during rinsing with the cold water flow meter (B8). |
107 | FM milk pump calibration. The milk pump was measured during cleaning. |
108 | MS milk pump calibration. The milk pump was measured during cleaning. |
110 | Temperature sensor on the right in the cooling unit. The right temperature sensor in the cooling unit has been interrupted. |
111 | Temperature sensor on the right in the cooling unit. The right temperature sensor in the cooling unit has been interrupted. |
112 | Interruption at left temperature sensor in cooling unit. The left temperature sensor in the cooling unit has been interrupted. |
113 | Temperature sensor on the left in the cooling unit. A short circuit has occurred at the left temperature sensor in the cooling unit. |
115 | Steam thermoblock. Heating tendency recorded. |
116 | Milk thermoblock regeneration. Milk thermoblock high-temperature regeneration: heating time. |
117 | Milk thermoblock regeneration. Milk thermoblock high-temperature regeneration: cycle time. |
118 | High-temperature regeneration failed. The high-temperature regeneration of the milk thermoblock has failed. |
120 | Clean agitator. Water flow of the powder system is disrupted. Please clean coffee machine and restart the system if necessary. – Check the water circuit for the powder system – Clean the mixing chamber – Clean the coffee machine with cleaning program The door must remain open for at least 20 seconds for the message to disappear. |
149 | Error on the add-on unit. Please observe the error message on the add-on unit's display. |
290 | RFID module communication. The coffee machine's connection to the RFID module has been interrupted or the RFID module is malfunctioning. |
291 | Error on the touchscreen. The touchscreen does not function. |
292 | Error on the touchscreen fixed. The touchscreen can be operated again. |
293 | Hardware or software error on the touchscreen. Hardware or software error on the touchscreen. There is no driver for the touchscreen. |
294 | No audio files found. The search for audio files failed. |
295 | Event 295. |
302 | Communication UPC. The process PCA has not responded within the specified time. |
306 | Old software for process PCA. The software version of the process PCA is out-of-date. The process PCA remains in the Reset state. |
308 | Communication P3C. The PIC has not responded within the specified time. |
309 | Automatic restart. The machine is restarted automatically. |
320 | Spout motor incremental sensor. No signals have been received by the spout motor incremental sensor. |
321 | Spout motor incremental sensor. No signals have been received by the spout motor incremental sensor. |
322 | Unknown hardware version. Hardware versions are not compatible with one another. |
332 | I2C iQFlow communication. I2C communication between the coffee machine and iQFlow is not working correctly. |
333 | Flavor Station communication. The Flavor controller is not responding. Please check the connections between the coffee machine and the Flavor Station and make sure that the correct CAN ID is set. – Check the connection cable – Check the connection to other CAN nodes, Programming, Menu item 5.9 Individual outputs. |
335 | Cooling unit communication error. Cooling unit does not respond. Please check the connections between the coffee machine and cooling unit and make sure that the correct CAN ID is set. Check the connection cable – Check the connection to other CAN nodes, Programming, Menu item 5.9 Individual outputs. |
336 | Communication Foam Master. The milk controller did not respond within 10 s. Please check the connections to the Foam Master and the CAN ID. – Check the connection cable – Check the connection to other CAN nodes, Programming, Menu item 5.9 Individual outputs. |
337 | Communication Foam Master. The milk controller is not responding. The milk cleaning is canceled and the machine switches to energy saver mode. Please check the connections to the Foam Master and the CAN ID. – Check the connection cable – Check the connection to other CAN nodes, Programming, Menu item 5.9 Individual outputs A running milk system cleaning cycle is interrupted. The coffee machine switches to energy-saving mode. |
C:1 M:5 | Brew Chamber Glass. |
C:3 M:5 | Brew Chamber not Closed. |
C:40 M:5 | Flow Meter. |
C:50 M:5 | LIM Communication Error. |
C:20 M:2 | Information Missing. |
C:30 M:2 | Information Code. |
C:45 M:2 | Descale Finished. |
C:11 M:5 | Temperature Sensor. |
Parts Meaning
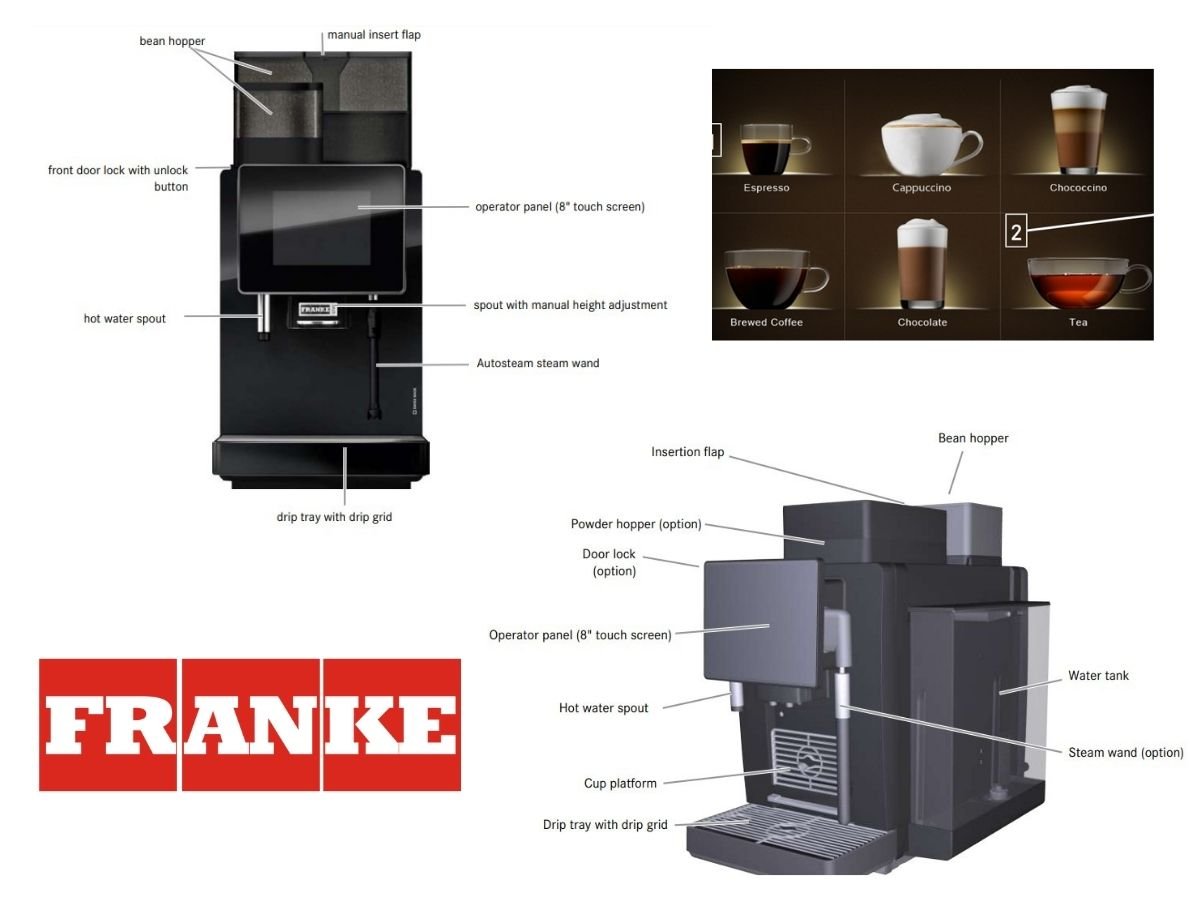
Troubleshooting
If an error occurs, a symbol on the dashboard is highlighted in a particular color, depending on the type of error. The user can tap on this to display a window with further information and troubleshooting instructions.
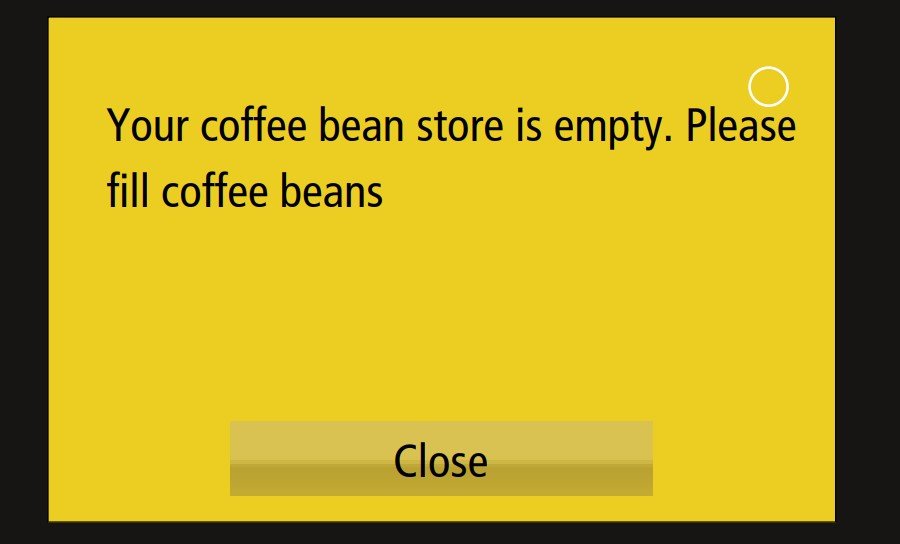
Problem | Possible Cause |
---|---|
Milk is frozen | Cooling unit target temperature is set too low. |
Cooling unit milk temperature is not being reached | Inadequate air circulation around cooling unit. Ensure that the required minimum clearance is present between the cooling unit and the wall (at least 50 mm) |
Descaler concentrate not being dispensed | Descaling cartridge seal is damaged or clogged or descaling cartridge is empty. Check the descaling cartridge fill level. Check the red adapter with the sealing ring and clear away any descaler crystals. Run the descaling process again. |
Descaling cartridge needs replacing despite not being empty | Descaling cartridge seal is damaged or clogged. Insert a new descaling cartridge, check the red adapter with the sealing ring and clear away any descaler crystals |
Touch screen not responding correctly | Machine software overloaded. |
Water level in water tank not being detected | Residual substances or deposits on the water tank's internal wall. Thoroughly clean and rinse out the water tank. |
No milk or just milk foam | Suction hose/milk line has a leak. Check the position of the spout insert and, if necessary, clean it. SU05 cooling unit: Check the O-ring on the suction hose coupling. Check the suction hose and, if necessary, replace it. |
Milk is not flowing correctly out of the milk spout | The milk spout was not installed correctly when it was last cleaned. Start the coffee machine cleaning process, and install the milk spout as per the instructions on the touchscreen. The milk spout is also part of the care kit. |
Coffee tastes stale | Grind too coarse. Select a finer grind Setting the grind coarseness. |
Coffee tastes strange | Minimal coffee usage. Pour a small amount of coffee beans into the bean hopper. |
Manuals Pdf
Franke BKON Troubleshooting.pdf