GE also known as General Electric is a leading appliance brand that is owned by Fujitsu General Limited. This Japanese original brand not only markets but helps manufacture and design humidity-controlling solutions, air conditioner units, washing machines, and other appliances that can be used in commercial and residential settings.
With manufacturing running in various parts of India, and Thailand the company has a great hold on local and international markets. Offering customers a taste of the best without breaking the bank. Making them one of the best choices that offer simple solutions that will change the way you lead your life.
Even the most reliable of appliances show error codes at times, so rather than panicking, we suggest you note down the issue and run it throughout the error code database for General Electric washing machines. Giving you direct access to the issue you are facing. Making sure you get the perfect solution without wasting time.
Front Load Washer Codes
Fault Codes | Solution |
---|---|
E22 | Fill timeout -No fill/slow fill. Fill time exceeds 8 minutes. Check water valve functions. |
E23 | Flood protect drain. In run state, any time the overflow be detected. Check water valve or water sensor. |
E31 | Drain timeout. Slow drain: 1. Machine will have water. 2 Not full. Check drain pump - t05. |
E38 | Dispenser error. Correct reservoir is not found and 8 switches are seen when motor is running. |
E39 | Dispenser timeout. No switches found in 45 seconds. Check dispenser - t12 |
E42 | Drive motor. Motor excess current draw. Check drive motor - t10 tumble, t11 spin, t13 spin. |
E45 | No speed feedback. Motor speed lost. Check Motor - t10 tumble, t11 spin, T13 spin. |
E46 | Drive motor - over temperature. Inverter over temperature. Power down (unplug) washer, wait 30 seconds and retry - use whites cycle sanitize temperature - if reoccurs, replace drive motor. |
E47 | Heat sink - over temperature. Inverter over temperature. |
E48 | Drive motor - open. Open motor phase. Check motor for open winding - if OK, replace inverter. |
E4A | Under volts. Under volts - DC bus voltage (inverter). Check Motor. |
E4B | Power up problems. Software/hardware problems. Check Motor or Motor windings. |
E4C | Over volts. Over volts - DC bus (inverter). Check Motor - t10 tumble, t11 spin, t13 spin. Power down (unplug) washer, wait 30 seconds and retry - if reoccurs, replace inverter. |
E50 | Drive/Control Interface system. Unexpected Motor Fault. |
E52 | Main control wake-up error. Lost communication between control and drive motor after initial success. Check connections/cables between main control and inverter. |
E54 | No motor response. Lost communication between control and drive motor. |
E56 | Electronic control. An unexpected reset has happened. Non-recoverable error. Main control board must be replaced. |
E57 | Checksum failure. Software error occurs - checksum failure. Non-recoverable error. Main control board must be replaced. |
E58 | Communication failure. Communication error occurs. |
E60 | Door lock switch failure. Switch failure occurs during lock. Power down (unplug) machine, wait 30 seconds and retry. Check wiring and connections between door lock. |
E61 | Door unlock and main control switch failure. Switch failure occurs during unlock. Power down (unplug) machine, wait 30 seconds and retry. |
E62 | System contact failure. Load failure occurs. Heater/pump/ pressure switch/ door lock/water valves/dispenser motor. |
E63 | Unexpected open door. Switch failure occurs during wake-up. |
E64 | Unexpected open door while running. Switch failure occurs during cycle. |
E65 | Water level sensor failure - foam. Pressure sensor frequency out of range. |
E66 | Water temperature sensor open. Water temperature sensor open. |
E67 | Water temperature sensor shorted. Water temperature sensor shorted. Check water temperature sensor - t07. |
NOTE: It’s important to note fault codes should only be used to help identify those components which require testing. Never replace a part based solely on an fault code. The control can generate a false fault if the right conditions exist . Use the code only as a reference and always check the component before replacing.
24 inch Front Load Washer
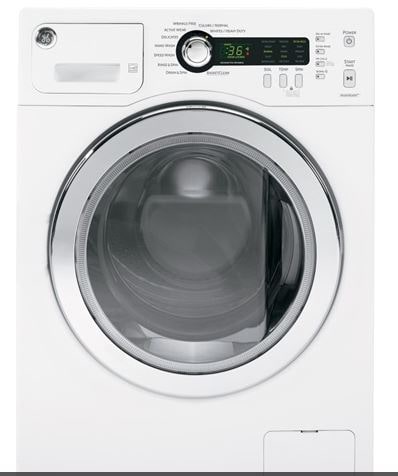
Error Code | Problem |
---|---|
E00 | No error |
4E | Water valve problem |
5E | Drain pump problem |
OE | Overflow level was reached |
HE | Heater relay error, replace the main pcb |
HE1 | Heater problem |
1E | Pressure sensor error |
LE | Leakage error |
9E1 | Under voltage error |
9E2 | Over voltage error |
3E1 | Motor start up failure |
3E2 | Over current error |
3E3 | Hall sensor error |
3E4 | IPM over heating error |
tE | Water thermistor error |
dE | Door open error |
dE1 | Door lock error |
dE3 | Door un lock error |
bE2 | Button error |
AE | Communication error between Main and Sub PBA |
SF | System Failure error |
DE2 | Door protection |
UE | Out of balance error |
27″ Top Load Washer
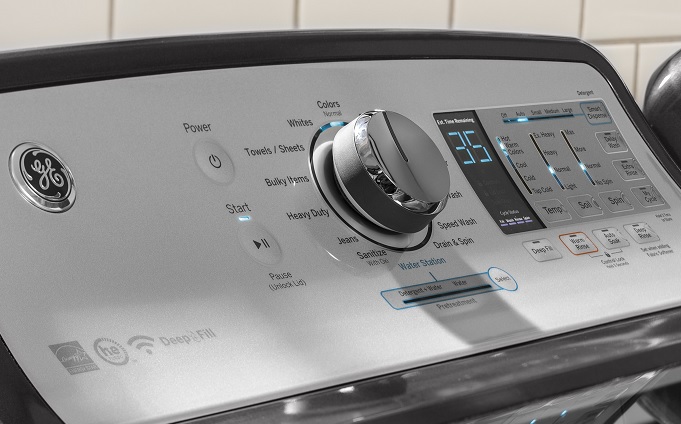
Fault Code | Problem |
---|---|
1 | Lock Monitor. |
2 | Lid Monitor. |
3 | Locked Rotor Monitor. |
4 | Reset Monitor. |
5 | Mode Shifter. |
6 | Critical Flood Level by Pressure. |
7 | Flood Warning Level by Pressure. Pressure level exceeds 16.5 inches above pressure port. Main micro received and extended period of pressure readings that is greater than maximum allowable fill volume. Pressure 16.5”. Voltage output must be present. Could mean water did get that high due to briefly stuck water valve. Voltage output of Sensor too high for actual water level because of sensor or water in pressure tube increasing pressure. |
8 | Pressure Sensor Loss. This determines if there has been a too great of a difference in the pressure sensor reading and the expected pressure sensor reading for the amount of water the control calculated it has put in. It assumes there is a pressure leak, a clog in the pressure hose/system delaying the increase in pressure, or a significant amount water leaking out. |
9 | Lid Switch Redundancy. Start attempted for a 4th cycle when the previous 3 cycles have completed with backup micro seeing lid open. Could mean the switches didn’t occur or backup processor didn’t get the signal because of lack of connection. |
10 | Mode Shift Feedback Monitor. Signal feedback state from the mode shifter (agitate or spin) and the state requested by the control are not the same and the basket or agitator is rotating faster than 3-4 RPM. Agitate mode feedback signal is no voltage. |
11 | Clock Monitor. 1. AC power line frequency is not 60Hz. 2. Software failure. |
12 | Redundant Flood Condition. Backup Processor received an extended period of pressure readings that is nearing over-flow levels. Pressure 18.0 Voltage Output must be present. Could mean water did get that high due to briefly stuck water valve. Voltage output of Sensor too high for actual water level because of Sensor or water in Pressure tube increasing pressure. |
13 | Redundant Lid Unlocked. |
14 | Lid Lock Fault. Signal received by control is indicating the lock will not lock or unlock when requested or the lid switch is indicating open when the signal received indicated locked. |
15 | Water Temp Sensor Invalid. |
16 | Adaptive Drain/Slow Drain. The total number of times during machine life the actual amount of time the pressure sensor indicated the wash water had drained to empty exceeded the calculated time by the software. |
17 | Dry load sense times out and moves to the next part of the cycle selected. This occurs when the washer is not reaching the target speed within a defined time limit for the load type selected. |
18 | Drain Pump Clearing algorithm failed. While draining the pressure sensor value for water level did not indicate the washer was empty before the Max Continuous Drain ON time was reached. |
19 | UI State Time-out. Washer was paused for over 12 hours. This is normal operation. This will happen if the consumer and or control switched cycle to a paused state. |
20 | Critical Flood Level by Gallons. Water volume into the tub exceeded 41 gallons as calculated by the control. |
21 | Flood Warning Level by Gallons. Water volume into the tub exceeded 36.3 gallons as calculated by the control. Stops filling. |
22 | Out of Balance (OOB) during Dry Load Sense. Large wet/OOB load being washed. This is set if OOB condition is detected during dry load sense algorithm. Dry load sense will be abandoned and wet load sense will be started. |
23 | Critical Lid Lock. 1. Lock blockage 2. Lid Lock fault. Will not lock or unlock or is locked while lid is opened. |
24 | Lid Logic Failure. Lid switch fault. This fault is set if the system perceives the lid to be both OPEN and LOCKED for 5 consecutive seconds |
25 | Pressure Sensor Dropout. 1. Disconnected pressure hose. 2. Pressure tube is pinched or has water in it. 3. Pressure sensor fault. |
26 | Out of Balance (OOB) Ended Final Spin. |
Profile Front Load Washer
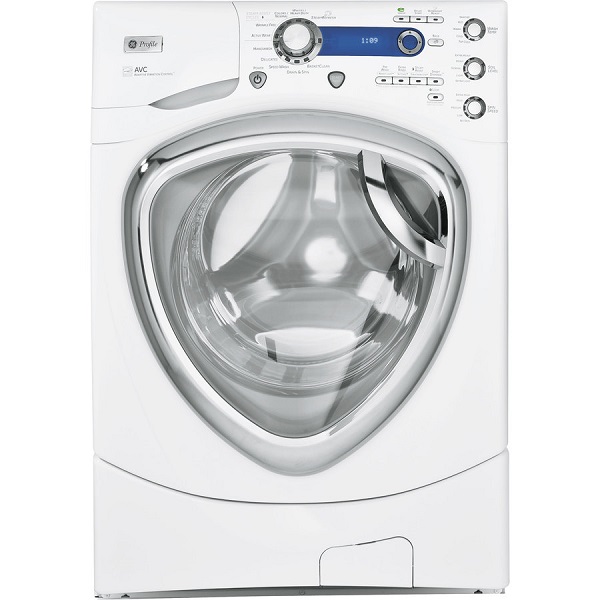
Error Codes | Cause |
---|---|
E1 | UI EEPROM. Internal problem with UI or MC board. Replace board as necessary. |
E2 | Power EEPROM. Internal problem with UI or MC board. Replace board as necessary. |
E4 | Thermistor Short. Water Temperature Sensor Problem. |
E5 | Thermistor Open. Water Temperature Sensor Problem. |
E6 | Pressure Switch. Water Level Sensor Problem. |
E7 | Slow Fill. Fill Problem. |
E8 | Drain System. Drain Problem. |
E9 | Dispenser Motor. Dispenser Problem. |
E10 | Motor Comm Interface. Communication Problem Between Main Control and Inverter. |
E11 | Door Lock. Door Lock Assembly Problems. |
E12 | Door Unlock. Door Lock Assembly Problems. |
E13 | Door Open. Door Lock Assembly Problems. |
E28 | Unexpected Door Unlock Detected. Door Lock Assembly Problems. |
E14 | Overflow Error. Overfl ow level was reached. |
E15 | Open Circuit. Open circuit in any of three motor phases detected. No speed info present and bridge will be turned off immediately. Motor will coast down. Drive will preserve nonzero speed info during the stop check stage. |
E16 | Over Trip. Inverter operation above design limits. |
E18 | Heatsink Over Temp. Inverter operation above design limits. |
E19 | Motor Over Temp. Inverter operation above design limits. |
E20 | Overload Current. Inverter operation above design limits. |
E21 | Overload Power. Inverter operation above design limits. |
E22 | Over Volts. Inverter Internal Problems. |
E23 | Under Volts. Inverter Internal Problems. |
E24 | Under Volts After Start. Inverter Internal Problems. |
E25 | Power Up. Inverter Internal Problems. |
E3 | Inverter EEPROM Fault Event. Inverter Internal Problems. |
E17 | ADC Fault Event. Inverter Internal Problems. |
E26 | LIN Comm Fail. There is a problem with the Communication between the Main Control and the User Interface Control. |
Profile DPVH880 Dryer Codes
E1: Interface EEPROM. Reading or writing improperly. Replace UI board.
E101: Power EEPROM. Reading or writing improperly. Replace power board.
E2: Inlet Short. Inlet thermistor shorted; check and replace if necessary.
E4: Inlet Open. Inlet thermistor open; check and replace if necessary.
E3: Outlet Short. Outlet thermistor shorted; check and replace if necessary.
E5: Outlet Open. Outlet thermistor open; check and replace if necessary.
E61: Check Electrical Connection. Input voltage too high; please check power connections.
E81: Power Model. No model select connector detected; check model selector on power board.
E10: Blower Motor. Blower motor is not rotating properly. Please check.
E11: Blocked Airflow. Check ventilation system.
E12: Drum Motor Motor is not rotating properly or centrifugal switch is bad. Please check.
E16: LIN Comm Fail. There is a problem with the communication between the machine control and the UI control.
E17: VFD Communication Error. There is a problem with the serial communication interface between the UI and the VFD.
E18: Stuck Button. Stuck keys. Please check.
Troubleshooting
Trouble | Solution |
---|---|
Small amount of water remaining in dispenser (on some models) at end of cycle | Normal dispenser operation. It is normal for a small amount of water to remain in dispenser after the cycle. |
Short spray and delay after pushing the Start button | Lid was opened and closed between cycle selection and start. This is normal. See START-UP SEQUENCE in the Safety Instructions section. |
Water level seems low | This is normal. Water may not cover the top level of the clothes. This is normal for this high efficiency washer. |
Low water flow | Water valve screens are stopped up. Turn off the water source and remove the water connection hoses from the upper back of the washer and the water faucets. Clean both the hose screens (if so equipped) and the screens in the machine using a brush or a toothpick. Reconnect the hoses and turn the water back on. Check to ensure there are no leaks at the connections. |
Water siphoning out of washer | Drain standpipe is too low or hose too far into standpipe. The drain hose must exceed 32” height at some point between the washer back and the drain pipe. Use anti-siphon clip. |
Water won’t drain | Drain hose is kinked or improperly connected. Straighten drain hose and make sure washer is not sitting on it. Top of drain outlet should be less than 6 ft (1.8 m) above floor. |
Washer spins and pauses at the beginning of cycles | This is normal. The washer is sensing the load. |
Residual powder in dispenser or clogging of dispensers | Wash water too cold or low home water pressure. Select a warmer wash temperature if possible to improve dissolving of detergent or use liquid detergent. Make sure siphon caps are free of debris and fully pressed into position. Remove and clean tray if clogging occurs. |
Laundry additives dispensing too soon | Overfilling of dispensers. Do not overfill or add water to dispenser. Select Deep Rinse option when using fabric softener |
Washer pauses during spin cycle. | This is normal. The washer may pause during the spin cycle to remove soapy water more efficiently. |
Detergent packets not dissolving | Laundry detergent packet placed in dispenser Laundry detergent packets should not be used in the dispensers. They should only be added directly to the wash basket following the manufacturer’s directions. |
Unexplained time and/ or settings changes | Changing options (on some models) This is normal. Several options will change other options to maximize washer performance |
Basket seems loose | Basket moves or rotates freely. Washer basket does not have a traditional brake. Washer basket will move freely. This is normal. |
“Click” when water stops filling | Relay switch. The relay makes a click sound when activated. The water level activates the relay and stops filling. |
“Clicking” behind Control during fill | Automatic Temperature Control Valve. Two valves mix cold and hot water. The “clicking” is when either valve turns on or off to raise or lower the fill water temperature. |
Water flow changes during fill | Automatic Temperature Control Valve. Two valves mix cold and hot water. The “clicking” is when either valve turns on or off to raise or lower the fill water temperature. |
Motor sounds during spin | Motor ramping up/down during spin cycle. The motor will speed up incrementally during the spin cycle. When spin is complete, it will coast until it stops. |
How do I Reset my GE Washing Machine?
1.Unplug the washer for 1 minute from the electrical outlet.
2.Plug the washer back in and lift and lower the lid 6 times within a 12 second period.
- You have 30 seconds to start lifting and lowering the lid.
- The lid must be raised a minimum of 2″ ensure the magnetic connection on the lid is interrupted.
- Make sure you close the lid completely each time.
3.The motor has now been reset and is ready for you to start a cycle.
Control Panel
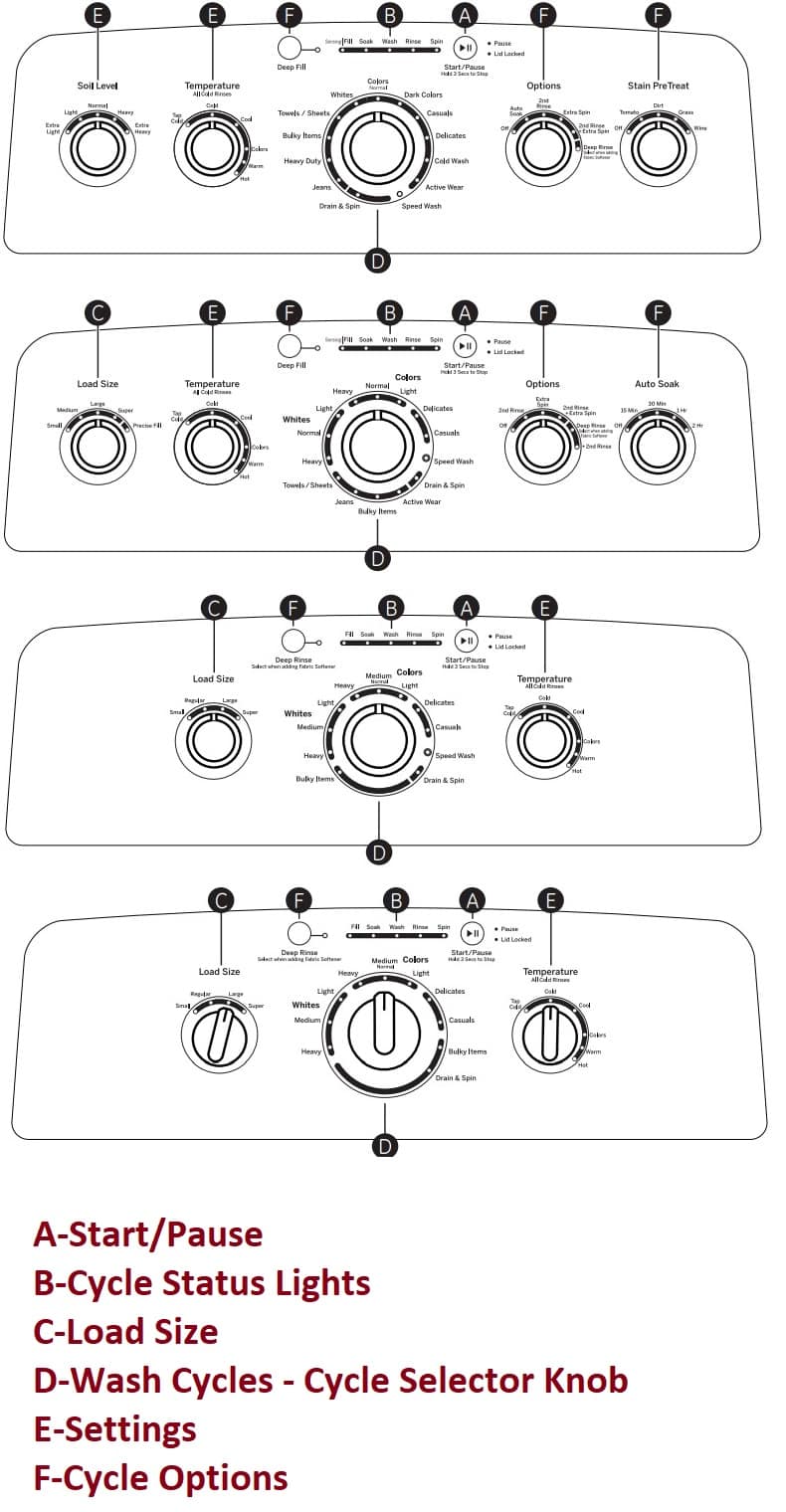